
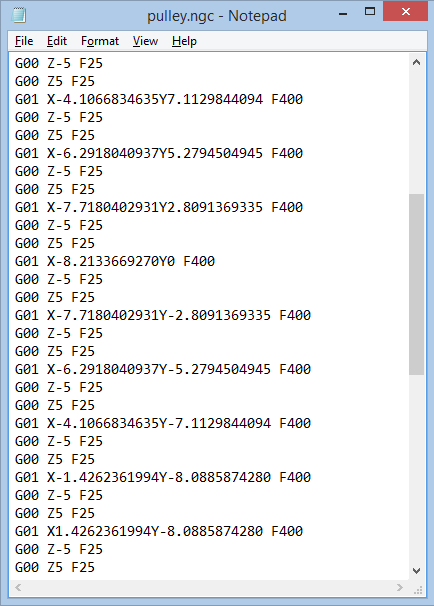
This 5-axis configuration comes at a higher cost due to the higher levels of calibration and automation technology needed to run the CNC machine and input the commands. The specific configuration of the machine or CAD design determines which two of the three additional rotational axes are used. The A, B and C axes move independently to the X, Y and Z in a rotating fashion. These axes work alongside X, Y and Z in rotational angles to deliver a 5-axis cutting machine capable of intricate designs while remaining a very high quality to the finished piece. However, 5-axis CNC machines use further axes, to implement into the cutting process from additional angles, giving greater scope for more complicated and intricate designs. A program is then produced in G-Code format, which feeds instructions directly to the CNC machine.Ĭurrently, it is most common for CNC Milling machines to have three axes to work from, X, Y and Z.
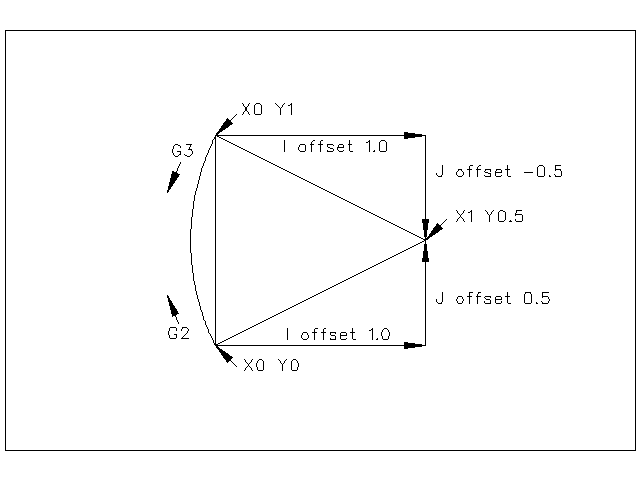
The shape is predetermined by the original CAD (Computer-Aided Design) file. In CNC machining, a part is formed using cutting tools and subtractive machining technology, which cuts away at the workpiece to create the desired shape. Efficiency and single set-up for manufactured parts are the main reasons why industries choose to implement 5 Axis CNC machining. The machines can be configured in such a way as to reduce the need for constant supervision. This article highlights the features of 5-axis CNC Machining and why it differs from 3-axis or 2-axis machining and notes the benefits of using a 5-axis CNC machine.ĭue to the increased number of axes, five-axis milling machines have greater capabilities than their three and two axes counterparts.
